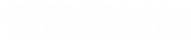
汽車內飾面料產品的制造工藝是什么
發布時間:2022-02-09 14:17:35 | 次瀏覽
汽車內飾面料是道路運輸產業用紡織品的關鍵細分化類別。隨著汽車工業的發展趨勢,汽車內飾面料的設計產品研發與生產加工都獲得了長足的進步。尤其是近幾年來,在化工工藝、新型材料、紡織業新技術、高端裝備等專業領域的創新驅動發展下,汽車內飾面料商品的生產制造加工工藝、研發能力和技術武器裝備水準都獲得了較大幅度的提高,新品、新技術新工藝和新技術層出不窮。
內飾用纖維原材料生產制造加工工藝
汽車內飾面料的原料以有機化學纖維為主導,在其中聚脂長絲占有率超出95%,短纖紗運用較少;一部分內飾面料中會小量應用羊毛絨等純天然纖維及其腈綸、丙綸布等化學纖維原材料。現階段,內飾纖維原材料的智能制造技術關鍵聚集在源液上色纖維、性能卓越纖維、循環利用纖維、多元化纖維及其生物基材料等行業。
源液上色纖維
汽車內飾面料的著色方法一般有3種,即棉紗上色、面料染色和源液上色。前2種著色加工工藝較為常見,但無論是棉紗上色或是面料上色都是會耗費很多的水、電、汽等電力能源,且有很多污染物質的排出,在節能減排、環境保護不容樂觀的時下,源液上色纖維的開發設計運用將變成汽車內飾面料未來發展發展趨勢。依據要求制取塑料母粒,將色母粒依照一定百分比的加入量與聚酯切片混和熔化,根據絲桿壓擠開展紡紗,制取出有色板塊聚脂長絲,再依據設計方案必須開展氣體形變或是假捻形變,可以制取出源液上色的空變絲(Air Textured Yarn,ATY)或是低彈絲(Drawn Textured Yarn,DTY)。本色上色技術制取的有色板塊纖維,其色調批號一致性、可靠性好,合適大批的生產加工,磨擦、耐光性水洗色牢度特性出色,與此同時不用上色生產加工工藝流程,全部生產制造全過程低碳環保、節能降耗環保節能。源液上色纖維合適大批化的生產制造,針對多種類小批量生產的變換靈便度受到限制,開發進度相對性較長,成本費較高。現階段,源液上色纖維早已在大家、通用性、萬里長城、有利等汽車廠家內飾坐椅、門邊框面料中運用,頂篷面料中的使用較少。
性能卓越纖維
汽車內飾面料的應用場景具備獨特性,對內飾面料的功能規定也是有較大差別,例如超耐磨滌綸布纖維用以坐椅面料以達到其耐磨性必須;高耐光水洗色牢度抗紫外光纖維用以電動遮陽簾或是汽車儀表板覆蓋用面料,高彈力、高延展性纖維用以傾斜度很大的商用汽車頂棚及其凸凹彎度比較大的門邊框。運營客運車、校巴等專用汽車對內飾面料點燃特性擁有苛刻的規定,關鍵的衡量指標值有點燃速度、煙相對密度和極限阻燃等級;選用高阻燃等級能滌綸布纖維制取面料可以達到規范和條例規定。此外,將根據納米技術成鍵技術制取的功能母粒與聚酯切片熔化紡紗可以開發設計出具備不一樣額外作用的性能卓越聚脂纖維,如抑菌作用纖維、空氣負離子作用纖維、撥水纖維等。
性能卓越的智能化纖維也逐步在汽車內飾面料中獲得運用。例如,選用反光作用聚脂纖維可以開發設計出不一樣視覺體驗的反光面料用以定義車內裝飾中;為了更好地達到汽車內飾自然環境氣氛的必須研發具備光傳輸作用的纖維,如聚甲基丙烯酸甲酯PMMA塑料光纖,將其運用在針織紗大提花面料的研發中可以制取出具備閃光作用的內飾面料;還可以選用柔韌度更強的高透型熱塑性聚氨酯纖維制取閃光紡織物。除此之外,光致變色、熱掉色及遇水后掉色等智能化纖維也愈來愈多的被汽車內飾面料室內設計師所關心,并完成相應的展望設計方案與開發設計。性能卓越智能化纖維在汽車內飾中的運用還處于探尋環節,這種纖維本身特性特點與車配內飾原材料的技術規定、生產加工情況的配對性的問題還要做更深層次的科學研究。
回收利用再運用環境保護纖維
針對汽車材料的回收利用再運用,各個國家都擁有確立的政策法規規定,伴隨著社會發展擔當意識的提升和愈來愈嚴的政策法規管控,回收利用再運用纖維原材料深受車輛汽車廠家的親睞,在汽車內飾面料及零部件框架復合材質中獲得開發設計運用。極星Polestar Precept 概念車圖片中,坐椅紡織物應用100%綜合利用塑膠瓶制取的再造聚脂為原料做成,其毛毯面料則是以廢舊的魚網回收利用做成的滌綸纖維編制而成。全新奧迪A3坐椅面料中89%的纖維原材料為再造聚脂纖維,毛毯、保溫材料、吸音板等也都是有應用此原材料。
差異化纖維
伴隨著顧客對內飾商品視覺效果、觸感等認知品質感受要求的提高,不一樣手感、不一樣光澤度和具備豐富多彩視覺沖擊的汽車內飾面料商品變成開發設計發展趨勢。三角、平扁、十字等異型橫截面纖維、全消光高層次感纖維、超光亮纖維等愈來愈多的被運用到汽車內飾面料中。為了更好地授予內飾面料綿軟細致的舒適感,以83dtex/144f、167dtex/144f等細旦高孔聚脂纖維為原料,根據針織紗大提花或是織造針織品加工工藝制取出細旦高密的舒適金絲絨面料,奔馳s知名品牌汽車內飾坐椅、頂篷中即使用了該類面料;或是以島嶼纖維為原料,根據織造或是非織造鋪網扎針加工工藝,與此同時開展聚氨酯膠粘劑含浸和堿減輕開纖,制取具備高級綿軟手感的仿漆皮面料運用在中國高檔汽車內飾坐椅、門飾板、汽車儀表板和頂棚等地區,現階段合資和自有品牌車系中多有運用。此外,根據熱聚合共聚物等方法制取出具備優良吸水性能和質感的超仿棉聚脂纖維,用以仿棉型觸感內飾面料的開發設計;亦有選用具備高光亮的FDY 長絲為原料,開發設計出具備綢緞般光澤度和細致絲滑手感的仿綢緞內飾面料;還能夠根據棉紗色調與組織架構的恰當設計方案,完成面料隨角異色的豐富多彩視覺沖擊。在汽車外形設計追求完美高認知質量的趨勢下,綿軟舒適、細致絲滑的金絲絨類面料、綢緞面料及其仿漆皮面料,在未來的汽車內飾設計方案里將會變成發展趨勢。
生物基纖維
生物基纖維是至關重要的翠綠色、綠色環保和原料可再生型纖維,它也是將來汽車內飾面料纖維原料開發設計的主要方位。因為生物基材料本身耐溫性等物理化學特點及其汽車內飾面料較高的技術規范規定,促使生物基纖維在汽車內飾面料開發設計中的運用還具有一定的局限,伴隨著技術的發展趨勢,沒多久的未來生物基纖維原材料用以汽車內飾面料的開發設計將變成很有可能。
內飾面料織造加工工藝
常見織造加工工藝簡述
汽車內飾面料的常見織造加工工藝關鍵有針織紗和針織品2類,針織紗又可以劃分為針織紗平布、機織大提花、雙劍桿提花等;針織品可分成織造和緯編,依據型號的不一樣織造又可以分成單針床和雙針床2類,緯編可以分為圓機和橫機2類。
新式織造技術
1.細旦高密織造技術
原料細旦化和高密的組織架構是針織紗類汽車內飾面料開發設計的發展趨勢。基本的針織紗大提花面料經密在270~560 根/10 cm 范疇,應用的棉紗規格型號多見33.3~66.7 tex聚脂長絲。細旦高密織造技術應用的棉紗大小在8.3~16.7 tex,面料的上機操作經密在800~1 200根/10 cm,這類細旦高密紡織物在織造全過程中為棉紗張力傳感器尤為重要,與此同時要調節好生產車間的溫濕度記錄,降低靜電感應及毛絲問題發生。
2.雙經軸織造技術
針織紗類汽車內飾面料的開發設計中,依據顏色紋路和視覺沖擊的制定必須,常常會碰到選用2種大小、送紗量或是特性差別比較大的棉紗做為管紗,為了確保織造的順利開展,一般多選用具備2套送經設備的雙經軸紡織機開展織造。每件送經設備根據交流伺服電機、齒輪軸、后梁及其支撐力設備等實現操縱,雙經軸的放置可以是左右式,節省室內空間,還可以是前后左右并列式。極高經密的面料織造時,為防止出現管紗重疊問題,也常選用雙經軸加工工藝開展織造。雙經軸針織紗面料多用以汽車內飾坐椅上,奧迪車Q2坐椅上面有此織造技術制取的面料。雙經軸織造加工工藝相對性繁雜,過程控制規定較高,成本費也較高。
3.電子器件橫移快速織造織造技術
伴隨著經編機生產制造技術的發展趨勢,電子器件橫移組織慢慢代替了選用花盆底、打緯的腳踏式橫移組織。電子器件橫移快速織造織造技術可以完成花型圖案的隨意拆換,省時省力,可以提升花型圖案循壞的限定,在快速情況下平穩運作,這種全是具備腳踏式橫移組織的經編機所沒法達到的。電子器件橫移組織的運用為經編機完成快速高效率發展趨勢打下了技術基本。
4.大隔距間距紡織物織造技術
大隔距間距紡織物的織造技術主要是運用織造雙針床機器設備開展的,根據調節經編機前后左右針床間的隔距,可以達到不一樣壁厚的間距紡織物的織造。用以開發設計大隔距間距紡織物的經編機,一般多見6把或是7把梳櫛,前2把梳櫛用以整體面層織造,后2把梳櫛用以底邊織造,正中間2把或是3把梳櫛用以正中間連接層的成型。整體面層和最底層多選用聚脂DTY低彈絲做為原料,為了確保成型要求及間距紡織物的縮小回彈力等特性,多選用聚脂拉絲做為原料。車輛用大隔距間距紡織物的薄厚在4~10 mm范疇內,關鍵運用于坐椅面料或是自然通風坐椅框架、汽車儀表板或是門邊框底層等地區;還能夠根據強力膠或是膠紙復合型替代海棉,完成與紡織物面料或是皮革制品材質的雙層迎合。大隔距間距紡織物織造全過程的薄厚勻稱一致性操縱是關鍵和難題,薄厚不均勻會危害零部件成形和外型品質。一汽紅旗HS7汽車儀表板覆蓋中運用了此技術制取的間距紡織物。
5.飛織織造技術
飛織技術又被稱為走線技術,最開始運用在球鞋的開發設計中。飛織技術可以完成面料豐富多彩的機構紋路和構造轉變,授予面料很好的延展性、可塑性和出色的透氣性能。與此同時,運用飛織技術的成型特性,依據具體必須,運用自動式的電腦橫機,根據數據信息程序編寫和全自動編制,可以完成商品的一體成形,降低原來的剪裁與縫紉生產加工工藝流程,開發設計出半成型或是全成型的內飾飛織面料,創新原來的剪裁、縫紉等生產流程,完成汽車內飾件的半成型覆蓋或是全成型覆蓋。飛織織造技術的生產加工高效率相對性較低,可以用寬幅受到限制,加工工藝也比較繁雜,尤其是3D一體成形技術,成本費也較高,這也在一定水平上限定了其應用推廣。中國汽車廠家多選用飛織技術開展2D 平面圖紡織物的開發設計,且多以塑膠板材方式開展。
內飾面料印染加工工藝
染色技術
汽車內飾面料常用的紡織材料多見聚酯纖維面料,這就確定了其染色生產加工技術的獨特性。聚酯纖維面料吸水性差,分子式中缺乏活力官能團,分子結構排序密切,因而染色染在的困難比較大,必須在高溫的情況下開展。
1.超低溫染色技術
超高壓高溫染色技術,針對電力能源的使用量比較大,造成的污水污染物質也較多,染色成本費較高。減少染色溫度、降低耗能,減少染色成本費,一直是領域內設計的熱點話題。根據染色媒介的引進,染色溫度可以從現在的130~135 ℃減少到95~110 ℃,也可以得到比較好的染色實際效果和水洗色牢度。可是針對染色媒介的挑選和運用必須較為慎重,要考慮到媒介引進后對生態環境保護、商品安全健康的危害。
2.高耐光水洗色牢度染色技術
相較為家居家紡服飾商品,汽車內飾面料對耐光性水洗色牢度擁有很高的規定。針對染色面料而言,完成其較高的耐光性水洗色牢度作用必須挑選具備高耐光的染劑并相互配合適合的染色加工工藝,如前工藝處理、提溫速度、隔熱保溫時間及其后工藝處理等。一般情形下,增加染色隔熱保溫時間可以減少提溫速度,充足的預處理是確保染色勻稱性和染色色牢度的主要基準點。依據實際商品和加工工藝的必須,可以加上少量的日曬提高劑,提升企業產品的耐光性水洗色牢度。汽車儀表盤、電動遮陽簾、擋陽板及坐椅用面料多選用此染色技術,保證運用全過程中面料水洗色牢度符合要求。
后整理技術
1.常見的后整理技術
汽車內飾面料常用的后整理技術,主要包含熱定型、平幅水清洗、干洗店、機械設備預縮、汽蒸預縮、平幅氣旋洗、噴毛、修毛、磨毛等整理加工工藝,依據不一樣的商品特性及開發設計必須可以選用差異的組成加工工藝。
2.作用整理技術
汽車內飾面料的多功能性也是產品研發的關鍵。對面料開展阻燃性整理、防靜電整理、抗耐磨損整理、頂弄整理、綿軟整理、三防整理等,一般都能夠根據浸軋整理劑溶劑的技術執行。一部分商品必須開展各種作用累加的復合型作用整理,必須對改性劑的融為一體性及浸軋方法開展提升挑選,如阻燃性和三防整理,可以挑選相溶性好的2 種改性劑開展同浴一浸一軋方法開展,還可以選用分階段式開展整理。對內飾面料進行復合型作用整理是汽車內飾面料的使用發展趨勢,2020款榮威汽車RX5頂篷面料即選用復合型作用整理技術授予其抑菌、三防和阻燃性作用。
鍍層也是較常用的整理加工工藝,一般全是選用刮板式鍍層頭開展。鍍層膠的種類以油基的亞克力類和聚氨酯材料類為主導,亞克力最常見,聚氨酯材料類成本費比較高一些,但具備不錯的延展性。依據具體要求可以挑選對鍍層膠漿開展泡沫塑料生產加工,也可以在鍍層膠中添加無鹵阻燃劑、抑菌劑等新型功能材料,對面料開展多功能性的鍍層整理。
內飾面料后制作工藝近些年,汽車消費貸款人群展現低齡化發展趨勢,對內飾面料的要求也向著時尚化、人性化和高質量發展,愈來愈多的生產加工技術和加工工藝被運用到汽車內飾面料的開發設計中,為顧客帶來了更多層次多種感觀的使用價值感受。
1.數碼印花技術
數碼印花加工工藝因其所具備的生產制造高效率、開發設計方便快捷等特性,在民用型紡織業行業運用較多。因為高耐光水洗色牢度黑墨水技術的持續完善,數碼印花技術也逐漸慢慢在汽車內飾面料的開發設計中運用。除開在紡織物面料表面開展服裝印花外,還能夠在鍍層紡織物如PVC 人造皮革和PU pvc人造革上開展服裝印花。上汽汽車MG3概念車圖片坐椅面料曾運用過數碼印花技術;除此之外,在pvc人造革表面開展數碼印花也是汽車內飾原材料的開發設計發展趨勢。
2.激光打標技術
在仿漆皮面料或是金絲絨面料表面,運用激光器的熱裂功效,在紡織物表面產生特殊的花型圖案紋路,這一新技術也已逐漸在汽車內飾面料中應用。根據調節激光器的動能及速率等主要參數,可以完成激光打標紋路的濃淡及視覺效果質感。在PVC和PU革表面也可以開展激光打標生產加工。
3.溶接技術
將塑料材質與紡織業面料溶接,產生材料和色彩對比,也是現階段汽車內飾面料設計方案的一種自主創新技巧。這類技術,主要是選用熱固性的PVC或是TPU原材料,根據高頻機的功效完成其在紡織物面料表面的溶接。2020款一汽奔騰E01坐椅面料中運用了溶接技術。
4.熱印技術
將設計的花型圖案紋路手工雕刻成熱印平板電腦或是圓輥,在高溫和負擔的效果下,將模貝紋理燙印到紡織物或是皮革制品表面,授予紡織物和皮革制品3D立體視覺實際效果,這一加工工藝便是冷燙印技術。花型圖案紋路可以是特細紋路的線框,還可以是比較大的體塊,可以是平面圖直壓亦可以完成含有一定傾斜度或是傾斜度的立體式壓紋。熱印紋路的質感可以根據模貝中紋路的多少不一樣開展設計方案。熱印技術運用比較普遍,通過熱印的內飾原材料其運用早已從傳統的的坐椅面料拓展到門邊框、汽車儀表板、護欄等零部件地區。
5.層合技術
汽車內飾面料通常必須與海棉、間距紡織物或是無防布等開展雙層迎合后應用。常見層合技術主要是根據火苗復合型將海棉與面料迎合,伴隨著環境保護和氣味問題的突顯,選用水性膠水開展復合型或是選用PUR、PET熱溶膠開展雙層原材料的迎合變成發展趨勢。層合技術關鍵的側重點取決于迎合的色牢度及其對面料氣味性的危害。